An expedition canoe for Peter
We’ve started building a wooden canoe for Peter. Peter has been canoeing and kayaking for forty years now. He started with his parents when he was 8 and is still very passionate about it. He is what you might call a discerning customer who knows exactly what he wants. It sets the standard high for us and that just how we like it.
An asymmetrical canoe
A couple of years ago Peter bought the stations for an asymmetrical expedition canoe with the intention to build it himself. However, time, space and expertise were lacking. We now build the canoe in our shop with Peter’s assistance.
The boat is high volume, long (560 cm) and will be very fast but it is not for beginners. The rounded bottom lends to high speed but will also require some decent paddling skills. For high-speed transit across large bodies of water, with boat loaded or unloaded, this design is ideal.
The round bottom makes it fast, and it will have great final stability. The canoe will handle very well loaded. Even if Peter gets too enthusiastic and tips over, the hull design, the low profile tips and the light weight will make the canoe easy to right.
The stations
Unlike our own boats where we start with our own stations, this time we’re building with the stations provided to us by Peter. This requires some calculating and measuring to get them right and to figure out there position. We have a rough idea but setting up stations on the strongback should be done with great precision.
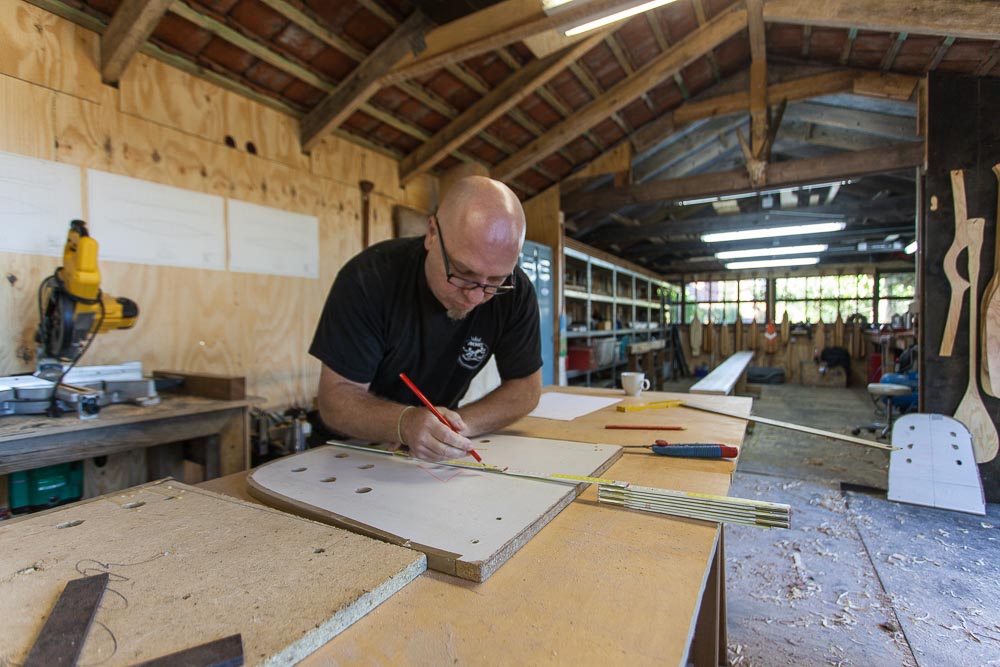
The strongback
Once the stations are ready they can be secured to the strongback. This is a very stable and strong work bench on which we will build the canoe. Attention to detail is required when building a canoe. We want to make sure the ultimate result is a straight canoe, you don’t want to paddle in circles.
Selecting the wood and ripping the strips
Peter wants to use western red cedar with details in ajous for his canoe. The contrast between both woods is very appealing. Ajous is very light while cedar has a warm redish glow. Both woods are lightweight, flexible and available in long lengths without knots. That makes them ideal for canoe building. We always personally select our planks at our local lumber yard. We want wood with straight grain and no discoloring.
Building a wooden canoe requires about 80 full length strips. We rip our strips ourselves and mill them with a bead-and-cove to make building easier and better.
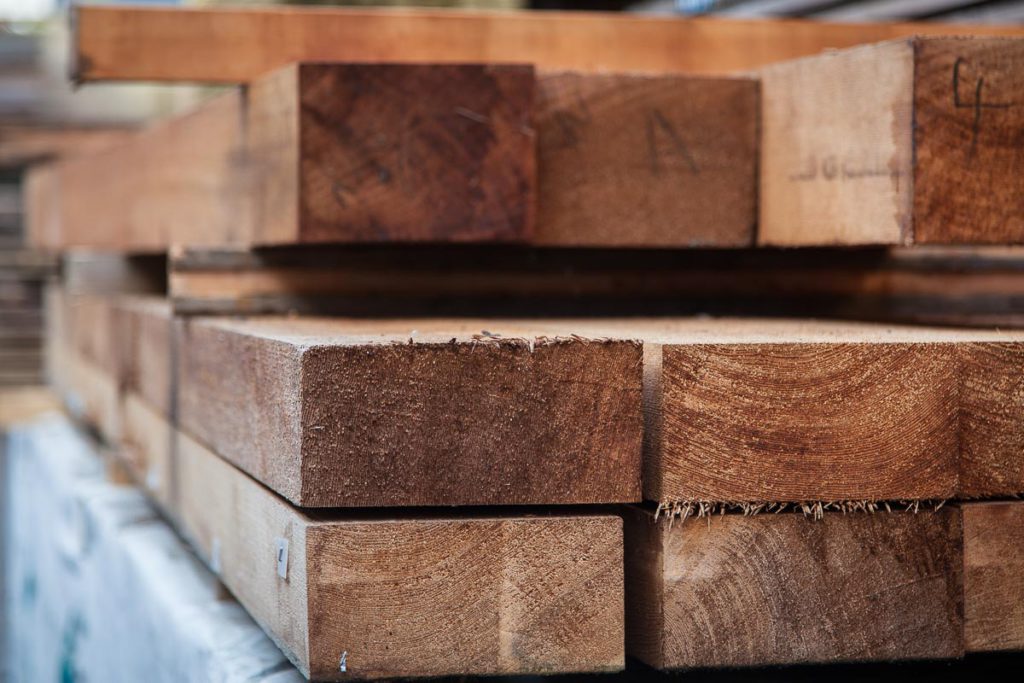
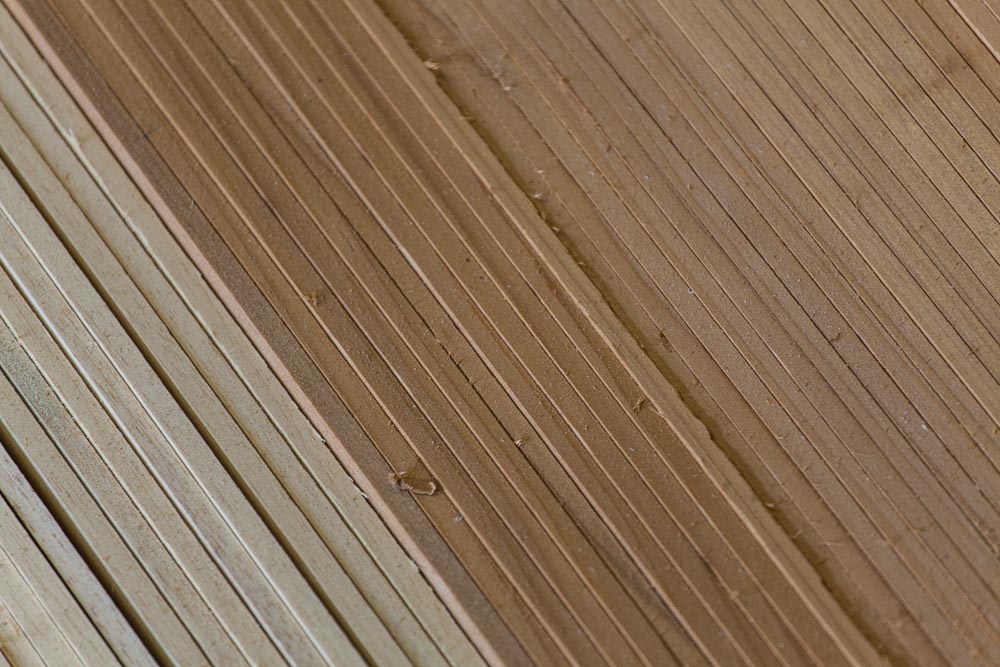

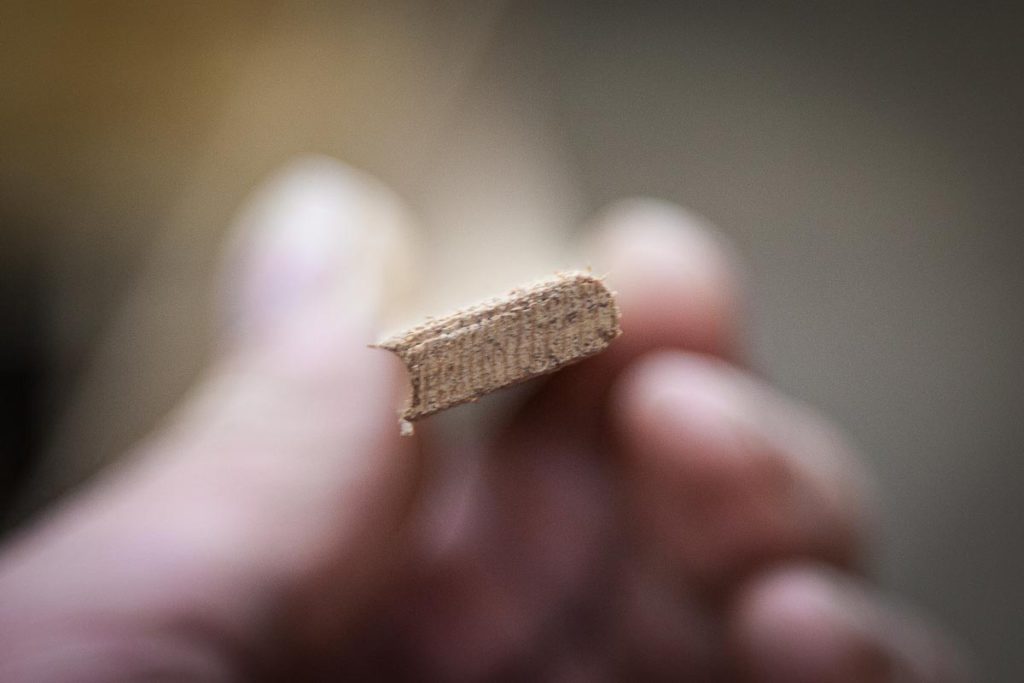
Installing the inner stems
Now that the strongback is ready and the stations have been installed we can start building. The first step is to install the inner stems. These are essential when building a wooden canoe. They form the spine of the boat. Stems are made up of laminated strips of ash. Because Peter’s canoe has a bow and stern with a very small radius we have to steam the strips before we can bend them.
Once dry and bended, they are glued together wit thickened epoxy resin.
Stripping the canoe
When you ‘re building a canoe the most exciting part is the actual building with the wood strips. Strip by strip the canoe materializes. Every strip is stapled to the form and glued together. In a couple of sessions your canoe becomes reality.
Sanding the canoe
Preparing the canoe to be laminated is a crucial step in the process of building a wooden canoe. first the staples have to be removed and prior to sanding the entire hull is planed. Sanding is done with an orbital sander.
Laminating the canoe
Strength and impermeability is added to the canoe by laminating the hull with glass fabric and 3 to 4 layers of epoxy. It’s also the moment you finally see the warm glow of the cedar and how the canoe will eventually turn out to look like.
Gunwales, seats and decks
The final step in the building process is the fabrication of the gunwales, decks, yoke, thwarts and seats. For this expedition canoe strength is of primary importance. All outfitting is made of ash. The decks are laminated with two strips of walnut.
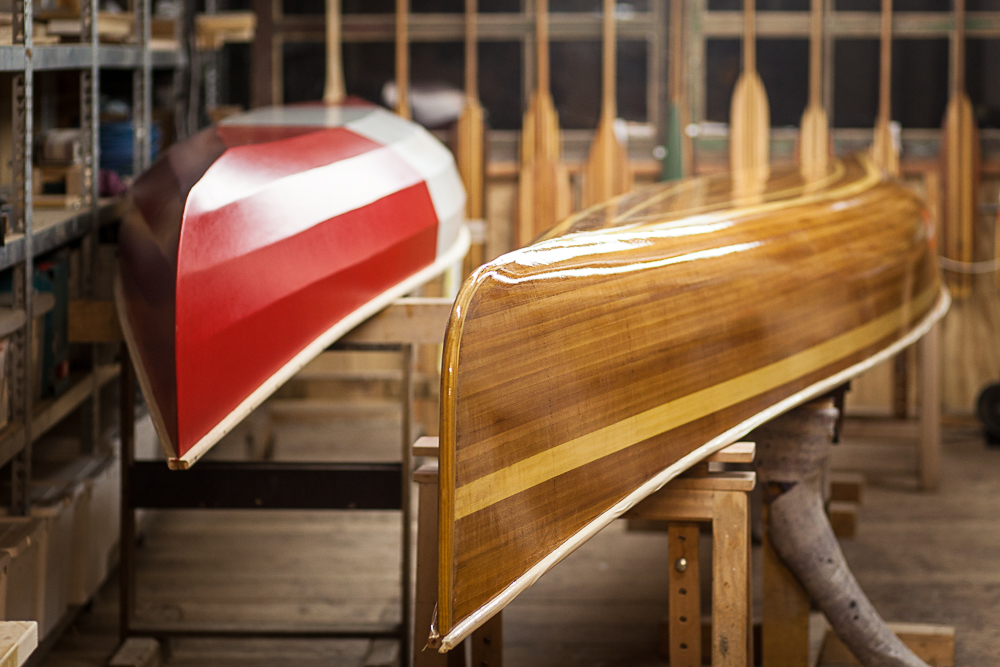
Launching
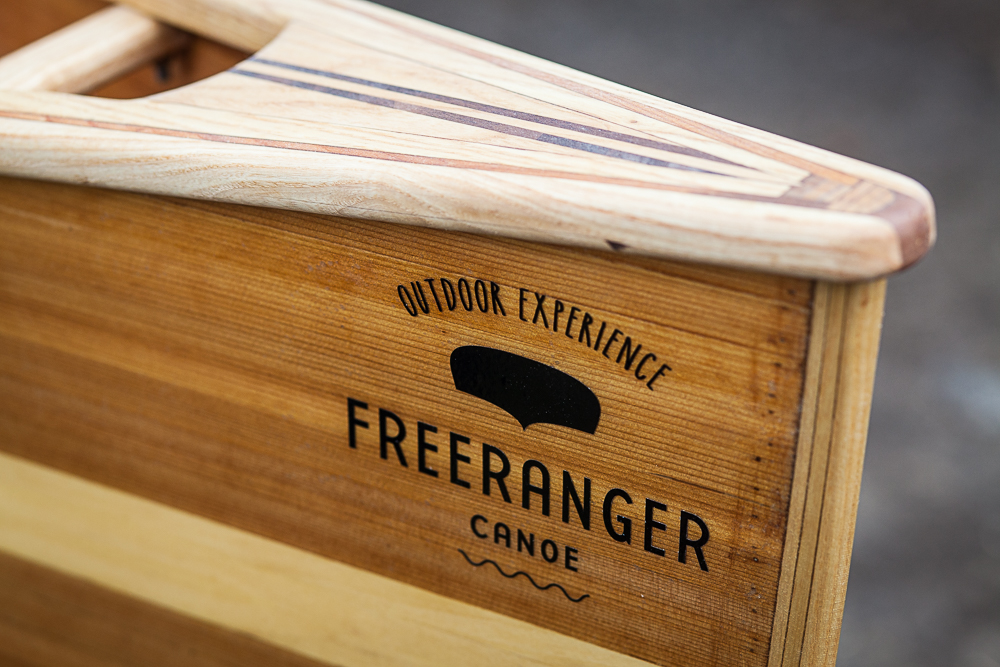
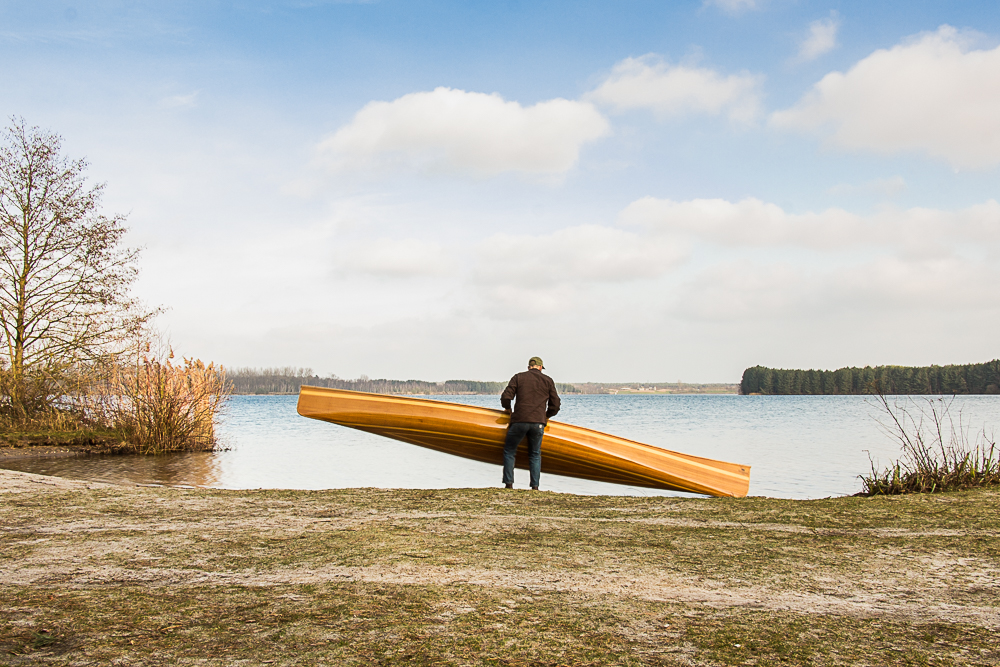
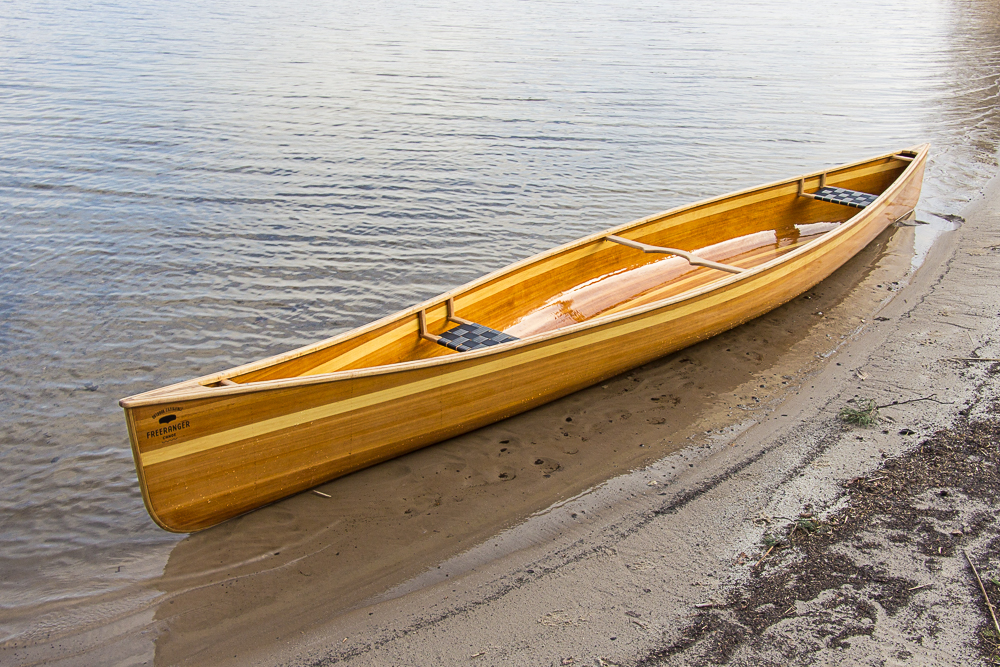
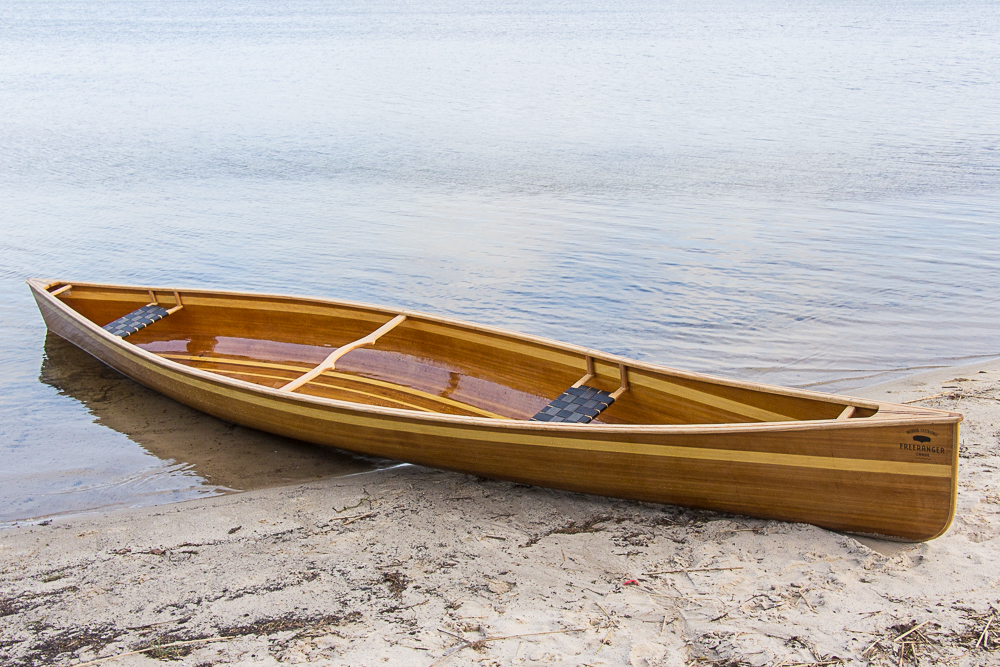
Amazing job! Very well explained, we love your handmade canoes
Congratulations!